製造業における金型について知っておきたい5つの重要ポイントーメリット・デメリット・外注選びー
第1章:金型とは?製造業における基本知識とその役割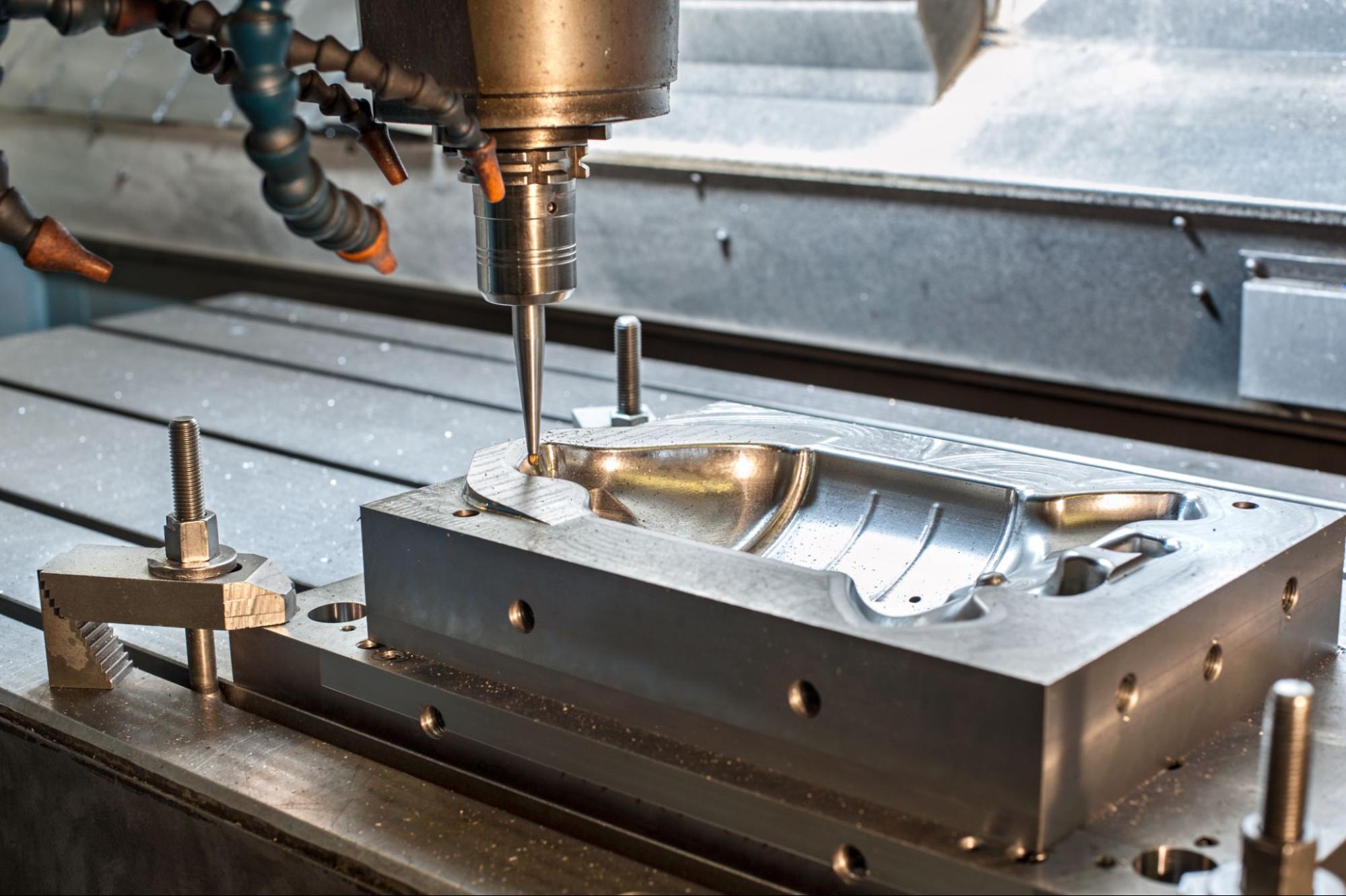
金型とは何か?
金型(かながた)とは、製品の形をつくるために使用される工具のことで、主に金属で作られています。製造業では、金型を用いてプラスチックや金属などを成形し、同じ形の製品を大量に生産するのが一般的です。私たちが日常的に使うスマートフォンのパーツや自動車部品、家電の外装など、身の回りの工業製品の多くが金型を使って製造されています。
金型の種類と用途
金型にはさまざまな種類があります。代表的なものには以下のようなものがあります。
- ・射出成形用金型:プラスチック部品を成形する際に使用される。
- ・プレス金型:金属板を打ち抜いたり曲げたりして成形するための金型。
- ・鋳造用金型:溶かした金属を流し込んで部品を成形するための型。
それぞれの金型は、製品の材質や形状、生産数量などに応じて使い分けられます。
金型の役割と製造業における価値
金型の最大の利点は、「同一形状の製品を高精度・短時間で大量に生産できる」ことです。この特性により、製品の生産性が飛躍的に向上し、製造コストの削減にもつながります。さらに、金型を使うことで、寸法のばらつきを抑え、製品の品質を一定に保つことが可能になります。
また、近年では金型の精度が格段に向上しており、ミクロン単位での加工も実現しています。これにより、デザインの自由度や部品の機能性が高まり、軽量化や複雑な形状の製品づくりも可能になっています。
金型設計に求められる専門性
金型の設計・製作には高度な技術と経験が求められます。製品の形状だけでなく、使用される材料の流動性、冷却の仕組み、抜きやすさ、耐久性など、さまざまな要素を考慮する必要があります。設計段階での判断ミスが、後の工程で不具合やコスト増につながることもあるため、慎重な対応が求められます。
さらに、金型の製作には数週間から数カ月かかることも珍しくなく、初期投資も高額になるため、小ロット生産や短納期案件では採用を見送るケースもあります。
製造業における金型の重要性
特に自動車、家電、電子部品、医療機器といった分野では、金型の有無が製品の競争力を左右する重要な要素です。製品の企画段階から金型の特性を踏まえて設計を行うことで、試作回数を減らし、量産体制へスムーズに移行できるようになります。
その反面、金型に関する知識が不十分なまま進めてしまうと、設計ミス、納期の遅れ、コストの膨張といったトラブルが発生しやすくなります。したがって、金型をただの「形を作る道具」と捉えるのではなく、製造全体の効率と品質を支える重要な要素として認識することが求められます。
第2章:金型導入のメリット:量産化によるコスト・品質面の効果
なぜ金型を使うのか?
製造業において金型を導入する最大の理由は、「同一製品を大量に、安定して、効率的に生産するため」です。手作業や汎用機械でひとつずつ部品を加工する場合、時間もコストも大きくかかります。それに対し、金型を使えば、1つの型をもとに製品を次々と成形できるため、生産スピードが大幅に向上します。さらに、高い寸法精度を保ちながら製品のばらつきを抑えられる点も、量産工程においては大きなメリットです。
生産コスト削減への貢献
金型の初期投資は高額ですが、中長期的に見れば1個あたりの製造コストが大幅に下がるのが最大の利点です。金型が完成すれば、その後は自動化された工程で製品を次々と成形できるため、人件費や加工工数を大幅に削減できます。また、製品の歩留まり(良品率)も高まるため、材料ロスの削減にもつながります。
特に1ロットあたり数千個、数万個の部品を生産するような現場では、金型の有無によって製品原価に大きな差が生まれます。量産を前提としたビジネスモデルでは、金型はコスト競争力を高めるための欠かせない武器になります。
高精度・高品質な製品の実現
金型による成形は、非常に高い精度で製品を作ることが可能です。特に近年では、金型加工技術の進歩により、ミクロン単位の精度が求められる部品にも対応できるようになっています。これにより、電子機器や医療機器など、極めて高い品質基準が求められる分野でも金型が活躍しています。
また、金型を使うことで、同じ設計・同じ寸法の製品を繰り返し製造できるため、出荷後のトラブルリスクが低減し、製品の信頼性向上にもつながります。製造業において「品質の安定」は、顧客満足やブランド価値を左右する極めて重要な要素です。
生産リードタイムの短縮
金型を使った生産工程は、熟練作業者による個別加工と比べて圧倒的にスピーディーです。成形・プレス・鋳造など、それぞれの工程で自動化が進んでおり、1個あたりの加工時間が数秒〜数分というレベルにまで短縮されることもあります。これにより、大量注文への即時対応や短納期案件にも柔軟に対応できる体制を構築できます。
加えて、金型を使用することで工程数がシンプルになるケースも多く、管理工数や工程間のロスも減らせます。これは製造現場の全体最適にもつながるメリットです。
製品設計の自由度向上
金型技術が進化したことで、以前は製造が難しかった複雑な形状や薄肉・軽量部品の成形も可能になっています。これにより、設計者が「作りやすさ」ではなく「機能性」や「デザイン性」を重視して製品設計を行えるようになり、製品開発の幅が大きく広がります。
特に、自動車の内装部品や家電の外装パーツなど、機能とデザインを両立させたい製品群では、金型の精度と成形技術が商品力を支えるカギとなっています。
第3章:金型のデメリットと注意点:導入前に知っておくべきリスク
初期コストの高さ
金型を導入する際、最も大きなハードルとなるのが「初期投資の大きさ」です。金型の設計・製作には専門的なノウハウと高精度な加工技術が求められ、その分コストも高額になります。特に複雑な形状や高精度が求められる金型は、数百万円から数千万円規模の費用がかかることも珍しくありません。
そのため、製品の販売数量が見込めない場合や、試作段階の製品に対しては、金型を作る判断が慎重になります。初期投資を回収できるかどうかは、生産数量と製品単価のバランスによって大きく左右されるため、事前のシミュレーションが非常に重要です。
リードタイムの長さ
金型の設計から実際の製作完了までには、一定のリードタイムが必要です。シンプルな形状の金型でも数週間、複雑なものや多工程の金型では数か月に及ぶこともあります。そのため、短納期での製品開発を求められるケースでは、金型製作が全体スケジュールのボトルネックとなる可能性があります。
また、設計ミスや仕様変更が生じた場合には、その都度金型の修正が必要になり、さらに時間とコストが追加で発生します。こうしたリスクを抑えるためには、製品設計の段階から金型製作を見据えた開発体制を整えることが欠かせません。
柔軟性の欠如
金型は「一度作ると簡単には変更できない」という性質があります。そのため、製品仕様の変更やマイナーチェンジが頻繁に発生するような製品には向いていません。一部の形状を変更するだけでも、金型を部分的に改造するか、最悪の場合は新たに作り直す必要があるため、柔軟な対応が難しいのです。
試作や少量生産の段階では、3Dプリンタや簡易金型、切削加工など柔軟性のある工法を採用し、本格的な量産段階に移るときに金型を導入するという判断も、選択肢として考える必要があります。
メンテナンスと劣化のリスク
金型は長期にわたって使用されることが前提ですが、使い続ければ当然摩耗や劣化が生じます。特にプレス金型や射出成形金型など、繰り返し大きな力や熱がかかるものでは、定期的なメンテナンスが欠かせません。メンテナンスを怠ると、製品の品質低下や寸法不良につながり、最悪の場合は生産停止に至る可能性もあります。
また、金型の保管や管理にも注意が必要です。長期間使わない場合でも、サビや劣化を防ぐための適切な環境管理が求められます。金型は資産であると同時に、維持管理にコストがかかる設備であることを認識しておくべきです。
導入判断には全体視点が必要
これらのデメリットを踏まえると、金型の導入は単に「便利だから」「大量生産に向いているから」という理由だけでは決められません。製品のライフサイクル、設計変更の可能性、想定ロット数、コスト回収期間など、複数の視点から慎重に判断する必要があります。
また、製造業では「金型を作るか作らないか」という判断自体が、開発スケジュールや全体の利益構造に大きな影響を及ぼします。したがって、金型導入の是非は経営層や開発部門、製造部門など複数の部門で協議することが望ましいといえます。
第4章:金型導入・製作の流れと失敗しないためのチェックポイント
金型導入の全体プロセス
金型の導入は、製品の試作が完了し量産体制に移行する際に本格的に始まります。しかし、実際には製品設計の初期段階から金型のことを意識したものづくりが求められます。製品がどのように成形されるかによって、金型の構造や加工性、耐久性が大きく左右されるためです。
一般的な金型導入のプロセスは、以下のようなステップで進みます。
- 1.製品設計・仕様決定
2.金型設計(構造・材質・成形方法の決定)
3.金型製作(加工・組み立て・仕上げ)
4.トライ&修正(試作成形・不具合の調整)
5.量産開始(本番成形・品質確認)
それぞれの段階で適切な判断と管理が求められます。特に初期段階での仕様決定と設計精度が、その後の工程の効率と製品の出来栄えを大きく左右します。
製品設計時に注意すべきポイント
製品の設計時には、「金型で量産すること」を前提とした設計を行う必要があります。これを「金型フレンドリー設計」と呼ぶこともあります。たとえば、以下のような点が重要です。
- ・アンダーカット(型から抜けない形状)の回避
- ・適切な抜き勾配の設計
・肉厚の均一化とヒケ防止
・成形材料の流動性を考慮したゲート位置の設計
これらを無視した設計を行うと、後工程で金型の製作が非常に困難になったり、成形時の不良が頻発する原因になります。そのため、設計段階から金型メーカーや成形メーカーと連携をとることが望まれます。
金型製作時の要点
金型製作は、非常に精密な加工を必要とする工程です。微細な寸法のズレや加工精度のばらつきが、そのまま製品の品質に影響を与えるため、信頼できる金型メーカーの選定が重要です。
また、設計通りに金型を製作するだけでなく、「試作成形」によって、実際の製品として問題がないかを検証する必要があります。試作段階では、寸法精度だけでなく、成形時の樹脂の流れ方、冷却時間、離型性など、実運用に近い条件での確認が求められます。
この段階で問題が発見された場合は、金型に対する微調整(モディファイ)や部分修正が行われます。時間とコストはかかりますが、ここでの手間を惜しむと、量産時に大きなトラブルとなって跳ね返ってきます。
よくある失敗例とその対策
金型導入の現場では、以下のようなトラブルや失敗がよく見られます。
- ・設計変更が頻発し、金型修正が何度も必要になる
・製品設計にアンダーカットや過剰な肉厚があり、離型できない
・材料特性を考慮せず、成形不良が多発
・金型の冷却効率が悪く、成形サイクルが長くなる
・トライ成形を十分に行わず、不良率が高止まり
これらを回避するためには、初期の設計品質の確保と、製作途中での密なコミュニケーションが不可欠です。特に、設計者と金型メーカー、成形現場の三者が情報を共有しながら進めることで、問題の発見と解決を迅速に行うことが可能になります。
チェックリストで進行管理を徹底する
金型導入のプロジェクトは、工程ごとに複雑で、多くの関係者が関わるため、チェックリストを活用した進行管理が効果的です。以下のような観点での確認が重要です。
- ・製品仕様と金型設計の整合性はとれているか
・トライ品の測定結果と要求精度は一致しているか
・金型のメンテナンスや予備部品の手配は済んでいるか
・成形条件の標準化は完了しているか
こうしたチェックを各段階で徹底することで、金型導入によるトラブルを未然に防ぐことができます。
第5章:金型の外注先選びと自社に合った導入判断のヒント
金型は内製か?外注か?
製造業における金型の調達手段としては、大きく「内製(自社で設計・製作)」と「外注(専門メーカーに依頼)」の2つがあります。大手メーカーなど、設備や人材が整っている企業であれば金型を内製化するケースもありますが、多くの中小企業では、外注による金型製作が一般的です。
外注には「専門性の高い技術を活用できる」「自社リソースを他の業務に集中できる」といったメリットがある一方で、「品質や納期のコントロールが難しい」「依存度が高くなりやすい」といった懸念点も存在します。そのため、外注を選ぶ際には、信頼性の高いパートナー選びが極めて重要となります。
金型メーカー選定の重要ポイント
金型を外注する場合、どのメーカーに依頼するかによって、その後の製品品質や量産体制の安定性が大きく左右されます。選定時には以下のような点をチェックすることが重要です。
- ・技術力と実績:過去の製作事例や対応可能な製品分野を確認し、自社製品との親和性をチェックする。
・納期対応力:短納期の実績や、トライ成形から量産立ち上げまでのスピード感。
・コミュニケーション力:仕様変更やトラブル時に、柔軟かつ迅速に対応してくれる姿勢。
・品質管理体制:検査・測定体制、トレーサビリティの有無など。
・コストバランス:単なる価格の安さだけでなく、初期費用と維持コストを含めた総合的な費用対効果。
また、初回の打ち合わせ段階で「要望にどこまで耳を傾けてくれるか」「提案力があるか」など、やり取りの質も評価材料となります。
よくある外注トラブルとその回避策
外注による金型製作では、以下のようなトラブルが発生することがあります。
- ・要件の伝達ミスによる金型の設計不備
・見積もり段階では想定していなかった追加費用の発生
・トライ時に不具合が見つかり、納期遅延に発展
・成形時の歩留まりが悪く、量産後に追加修正が必要
こうしたトラブルを避けるには、事前の情報共有を徹底することが何より大切です。製品仕様や要求精度、使用材料、成形機の条件などを具体的に共有し、書面に残すことがポイントです。可能であれば、設計段階から金型メーカーと協議を行い、成形性や金型構造についてアドバイスをもらうのも効果的です。
自社にとって「適切な導入判断」とは?
金型の導入判断においては、「自社の製品やビジネスに本当に必要か?」を多角的に検討することが重要です。以下のような観点で整理すると、導入の是非を判断しやすくなります。
- ・生産数量と初期投資の回収見込み
少量生産であれば、金型を使わずに加工で対応する方が合理的な場合もあります。 - ・製品ライフサイクルの長さ
仕様変更が多い製品や短期間でモデルチェンジする製品では、金型投資の回収が難しい場合があります。 - ・求められる品質レベル
高精度・高再現性が求められる場合は、金型導入の価値が高まります。 - ・社内の技術・人材・管理体制
外注するにしても、最低限の技術的知識や管理体制がないとトラブルを回避できません。
これらを総合的に判断し、「今の自社にとって、どの段階で金型を導入するのがベストか」を検討することが、製造業としての健全な投資判断につながります。
導入判断は「戦略的」に行うべき
金型は、単なる“製造設備”ではありません。コスト削減や品質向上、生産性の改善、納期短縮といった経営課題の解決に直結する「戦略的な設備投資」です。だからこそ、「とりあえず必要だから導入する」のではなく、事業計画や製品戦略と整合性のある形で検討し、活用することが求められます。