プレステンパーとは何か徹底攻略!導入前に押さえておきたいリスク管理と成功事例
1. プレステンパーの基本と仕組み
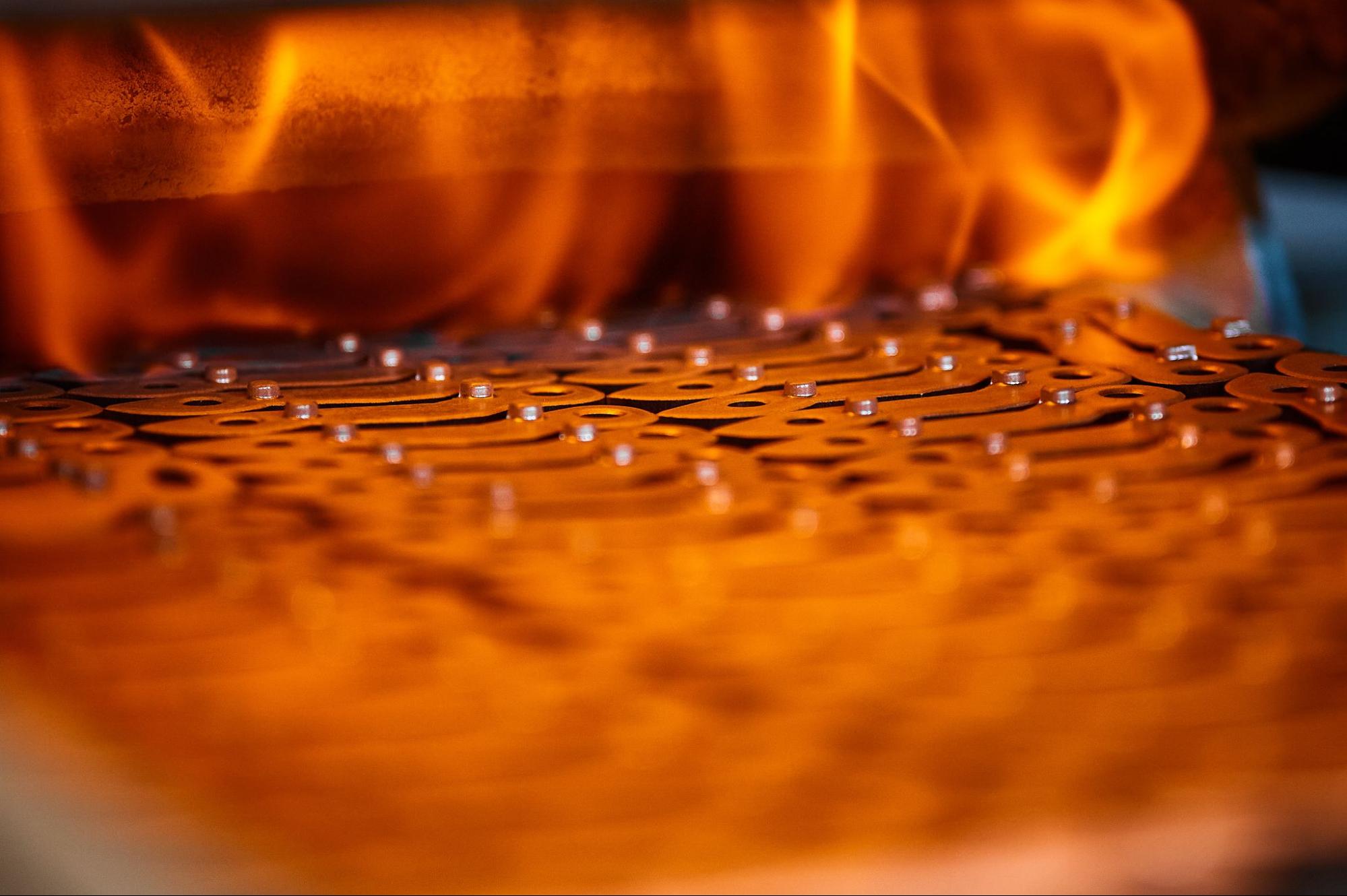
プレステンパーとはどんな熱処理か
プレステンパーとは、主に金属材料に対して行われる熱処理方法の一つで、「成形」と「焼入れ」を一連の工程で行う手法です。この工程は、自動車部品や航空機部品の製造など、耐久性や軽量化が求められる製品で広く用いられています。通常、金属は高温に熱せられた状態で成形を行いますが、プレステンパーでは成形後すぐに冷却することで硬化させ、強度や耐摩耗性を大幅に向上させます。このように、プレステンパーは製造工程を一括化し、素材の特性を最適化できる画期的なプロセスです。
プレステンパーの工程フロー
プレステンパーの主な工程は以下のようになります。
-
- 1.加熱
金属素材をおよそ900℃程度まで加熱し、塑性変形が可能な状態にします。この温度帯は素材の種類によって異なりますが、焼戻し温度を適切に管理することで、成形しやすい状態を保ちながら強度を高めることができます。
- 1.加熱
-
- 2.プレス成形
高温状態の金属を金型にセットし、短時間で成形します。この時点で形状が固定されるため、歪みが発生しにくいのが特徴です。金型に求められるのは、高精度な仕上がりを確保するための耐熱性と寸法精度です。
- 2.プレス成形
- 3.急冷(焼入れ)
成形直後に、金型を通じて急速冷却を行います。この冷却プロセスにより、金属内部の組織が「マルテンサイト組織」に変化し、非常に硬く、靭性(粘り強さ)を持った構造になります。これにより、優れた耐衝撃性や耐摩耗性が得られます。
使用される代表的な素材と用途
プレステンパーは主に高強度鋼(ハイテン材)と呼ばれる素材に対して行われます。高強度鋼は軽量でありながら、引張強度が高いため、自動車のボディフレームやバンパー、サスペンション部品などの安全性が求められるパーツで多用されています。また、航空機の部品にも採用され、軽量化と耐久性の両立を実現しています。
プレステンパーの重要性
プレステンパーは、製品の強度を飛躍的に向上させると同時に、製造工程を大幅に効率化できる技術です。特に従来の焼入れプロセスを個別に行う必要がなくなるため、生産コストの削減が可能です。加えて、プレステンパー技術は軽量化された車両や航空機の燃費性能を向上させ、CO2排出量削減などの環境負荷低減にも寄与しています。
しかし、工程中に発生する熱歪みや急冷による金属内部のストレスが製品不良の原因になる場合があります。そのため、適切な温度管理や、プレス機・金型の精度管理が不可欠です。
プレステンパーとは、高温で成形し、その直後に急冷することで金属の強度と耐久性を向上させる手法です。特に自動車部品や航空機部品など、安全性や軽量化が重視される分野で不可欠な技術となっています。効率的な工程による生産コスト削減や製品の高機能化を実現する一方、設備投資やプロセス管理が難しい点もあるため、導入時には十分な計画が求められます。
2. プレステンパーのメリットを理解しよう
強度向上効果の詳細
プレステンパーの最大のメリットは、成形と同時に金属の強度を大幅に向上できる点です。この技術では成形後すぐに急冷することで、金属組織が「マルテンサイト組織」という高硬度な状態に変化します。通常の焼入れと比較して、強度のばらつきが少なく、均一な性能を実現できます。
この強度向上効果により、部品の薄肉化が可能になります。たとえば、自動車のボディフレームを薄く軽量化できれば、車全体の重量が軽くなり、燃費性能が向上します。軽量化はただ単に燃費向上に寄与するだけでなく、車体が軽くなることで加速性能や操作性も向上するため、安全性と走行性能の両立にもつながります。
また、航空機部品や産業用ロボットのアーム部品など、耐久性と軽量化が求められる分野でも活躍しています。特に、機械的な負荷がかかる部品にとっては、耐衝撃性や耐摩耗性が向上することが重要であり、プレステンパーはこれらのニーズに応えられる技術です。
生産効率の向上
プレステンパーは「成形」と「焼入れ」を一連の流れで行うため、従来の熱処理工程に比べて作業工程が短縮されます。従来は、成形後に別途焼入れ炉を用意し、個別に熱処理を行う必要がありました。しかし、プレステンパーでは高温の成形からそのまま焼入れを行うため、中間工程の省略が可能です。
また、成形と同時に急冷することで、変形が少ない製品を安定して生産できます。従来の焼入れ工程では、急激な冷却による内部ストレスで部品が歪むリスクがあり、精度を求められる部品では再加工が必要になることもありました。プレステンパーを用いることで、歪みの発生を抑制し、高精度な部品を一度の工程で成形できるのは大きなメリットです。これにより、製造ライン全体の効率化が図れ、生産性が向上します。
さらに、プレステンパーは省スペースでの生産が可能です。従来の複数ステップを行うラインを構築する必要がなく、省エネ型の一体化設備を導入することで、作業環境をスリム化できます。これにより、製造現場の作業負担やランニングコストも削減されます。
コスト削減効果
プレステンパーは、長期的な視点で見た場合の製造コスト削減に大きく寄与します。従来の方法では、成形後に焼入れ炉に移送し、冷却を経てさらに仕上げの作業を行う必要がありましたが、これらの手間が省かれるため、工程ごとの設備や人員を削減できます。
また、部品の高強度化と軽量化を同時に実現できるため、素材の使用量削減も可能です。例えば、薄い板厚でも必要な強度を確保できるため、1枚あたりの使用金属量が減り、全体の生産コストが抑えられます。これにより、特に大量生産を行う自動車産業では、1台ごとのコストダウン効果が積み重なり、大きな利益改善につながります。
環境負荷の低減
生産効率が向上し、素材の使用量が減ることは、環境負荷の低減にもつながります。たとえば、車体が軽量化されると燃費が向上し、二酸化炭素(CO2)の排出量削減に寄与します。また、製造工程そのものの省エネ化により、工場全体の電力消費量を削減できます。
現在のものづくりにおいては、製品の性能向上だけでなく、**サステナビリティ(持続可能性)**を意識した製造プロセスの導入が求められています。プレステンパーは、従来技術と比較してエネルギー効率が高く、省資源型の製造技術として注目されています。これは、企業の社会的責任(CSR)を果たすうえでも大きなアピールポイントです。
プレステンパーのメリットは、強度向上・生産効率向上・コスト削減・環境負荷低減の4点に集約されます。自動車や航空機業界においては、軽量化と高強度化は安全性や性能向上のために欠かせませんが、その実現をシンプルな工程で行えるプレステンパー技術は、製造業の競争力強化にも貢献しています。
ただし、これらのメリットを最大限に活かすためには、適切な設備導入とプロセス管理が求められます。品質管理を徹底し、生産ライン全体を最適化することで、プレステンパー技術の恩恵を十分に享受できるでしょう。
3. プレステンパーのデメリットとリスク管理
熱処理後の歪みや変形のリスク
プレステンパーは成形と焼入れを同時に行うため、急冷時の内部応力によって金属が歪んだり変形したりするリスクがあります。この歪みの原因は、金属内部で急激に温度が下がる際、部位ごとに冷却速度が異なることで生じる応力の不均一性です。特に、厚みが不均一な部品や複雑な形状の部品は、歪みや変形が発生しやすくなります。
このリスクに対応するためには、以下の対策が有効です。
- ・金型設計の最適化:冷却時の熱分布を均一にするために、冷却水路を効果的に配置するなど金型設計を見直します。
- ・冷却速度の調整:素材に応じて急冷の速度を適切に調整し、内部応力の偏りを防ぎます。
また、製品が規格寸法を外れた場合、再加工や部品の廃棄が発生し、生産コストが増大する恐れがあります。そのため、冷却工程の管理が品質維持において非常に重要です。
設備導入コストの負担
プレステンパーを行うには、高温加熱が可能なプレス機や冷却機能付きの金型など、特殊な設備が必要です。これらの設備は初期導入コストが高く、特に中小企業にとっては負担が大きい場合があります。
また、プレステンパー専用のラインを新設する場合、プレス機の導入だけでなく、冷却システム、温度管理装置、排気設備などの周辺機器も必要です。設備費だけでなく、設置・メンテナンス費用が発生し、設備全体の総合的な費用を検討する必要があります。
・設備コスト削減のポイントとしては以下の方法があります。
- ・部分導入:全ラインではなく、試験的に一部のラインのみで導入し、効果を検証した後に本格導入する方法。
- ・中古設備の活用:信頼できる中古市場から設備を調達することで初期費用を抑える手法。
- ・国や地方自治体の補助金制度:新技術導入を支援する補助金や助成金を活用して導入費用を抑える方法もあります。
設備トラブルやメンテナンスの負担
プレステンパーラインは、加熱・プレス成形・急冷といった複数のプロセスが連動するため、設備トラブルが発生すると生産ライン全体が停止するリスクがあります。特に、冷却システムの不調は冷却不足や冷却ムラを引き起こし、部品が規格外品になる可能性があります。
トラブルの例としては、以下のようなものがあります。
- ・温度センサーの異常:適切な温度管理ができず、過熱や冷却不足が発生。
- ・冷却水漏れ:冷却システムの破損による急冷機能の低下。
- ・プレス機の摩耗:高温での連続稼働により、プレス機や金型の摩耗が進行し、成形精度が低下。
これらのリスクを最小限に抑えるためには、定期メンテナンスと予防保全が不可欠です。定期的な設備点検を行うことで、トラブルの発生を未然に防ぎ、生産停止による損失を回避できます。特に、温度センサーや冷却系統の異常検知システムを導入することで、設備異常を早期に発見し対応することが可能です。
熟練技術者の不足
プレステンパー工程は高温での作業を伴うため、高度なスキルと経験が必要です。特に、加熱温度や冷却速度の微調整、金型交換のタイミングなど、現場での適切な判断が求められるため、熟練した技術者の存在が重要です。しかし、現在の製造業界では少子高齢化の影響により、熟練技術者の人材不足が課題となっています。
この問題を解決する方法として、以下の取り組みが有効です。
- ・社内教育制度の充実:若手技術者の育成を目的とした研修プログラムの導入。
- ・自動化技術の導入:AIやIoT技術を活用して温度管理や冷却プロセスの最適化を図り、人の手を減らす。
- ・外部の専門企業との連携:新技術導入時に専門企業の支援を受け、ノウハウを社内に取り入れる。
また、最新のプレステンパー設備は、センサーやデジタル制御技術を用いて自動化が進んでおり、経験に頼らず再現性の高い製造が可能なシステムも登場しています。これにより、若手技術者でも品質の高い生産が行える環境を構築できます。
プレステンパーは優れた強度向上や生産効率化が可能な一方で、設備コストの高さや熱処理後の歪み、設備トラブルの発生リスクといった課題があります。また、技術者不足による運用面の不安も解決すべき課題です。
これらのデメリットを解決するには、設備の定期点検、効率的なライン運用、熟練者の育成、さらには補助金制度の活用など、包括的なリスク管理が必要です。特に、自社の製造工程や製品の特性に合わせたプレステンパー設備の選定が重要です。メリットとデメリットをしっかりと理解し、リスクをコントロールしながら導入を進めることで、長期的に高い成果を得ることができるでしょう。
4. プレステンパーの適用シーンと導入判断
プレステンパーが活躍する代表的な分野
プレステンパー技術は、主に以下のような高い強度と軽量化が求められる製品に適用されることが多いです。
・自動車業界
自動車のボディ構造には、乗員の安全性を確保しながら車体を軽量化するため、高強度かつ薄い鋼板が求められます。プレステンパー技術は、バンパー、ドアインパクトビーム、ピラー部分など、衝突時に外部衝撃を吸収しつつ車体を守る重要な部位に多く使用されます。軽量化が進むことで燃費が向上し、CO2排出量削減に寄与するため、環境規制の厳しい地域でも活用が進んでいます。
・航空宇宙産業
航空機の部品製造では、耐衝撃性や耐熱性に優れた高強度素材の使用が不可欠です。特に、エンジンカバーやフレーム部品は高い負荷がかかるため、強度を維持しつつできる限り軽量な部品が求められます。プレステンパーによる成形は、複雑な形状の部品でも精度を保ちながら高強度化できるため、航空機やロケット部品などの開発で活躍しています。
・産業用ロボットや重機部品
産業用ロボットのアームや重機のフレームなど、動力を効率的に伝達しながら耐久性が求められる部品にもプレステンパー技術が活用されています。強度向上によって部品の小型化が可能となるため、ロボットアームの可動域を広げたり、軽量化により駆動効率を高めることができます。
・スポーツ用品・アウトドアギア
スポーツ用品やアウトドア製品では、耐久性と軽量性を両立することが重要です。例えば、軽量な金属製のフレームや部品が採用されるテントのポールや自転車のフレームなどは、プレステンパー技術によって高い耐久性が実現されています。
他の熱処理方法との比較
プレステンパーは優れた技術ですが、他の熱処理方法との比較も重要です。以下は、代表的な熱処理技術との比較です。
熱処理方法 | 特徴 | メリット | デメリット |
焼入れ・焼戻し | 高温処理後に冷却し、必要に応じて再加熱する工程 | 強度と靭性のバランスが取りやすい | 工程が多く生産効率が低い |
低温焼入れ | 比較的低温で処理する方法 | 変形しにくく、ひずみが抑えられる | 強度向上効果が限定的 |
プレステンパー | 成形と焼入れを同時に行う工程 | 強度向上と軽量化が同時に可能 | 専用設備が必要で導入コストが高い |
プレステンパーは特に、生産性向上と製品品質の両立が必要な場合に有効です。従来の焼入れ法では別工程で成形・焼入れ・仕上げを行う必要がありますが、プレステンパーは一度の成形で済むため、時間やコストの削減が可能です。ただし、導入費用や運用管理の負担が高いため、用途に応じて他の方法と比較検討する必要があります。
プレステンパー導入の判断基準
プレステンパーの導入を検討する際には、以下のポイントを判断基準にすると良いでしょう。
① 製品の特性と要求性能
製品に高い強度、耐摩耗性、耐衝撃性が求められるかどうかが判断材料になります。特に、軽量化しながら高い安全性能を実現することが重要な製品(自動車のバンパー、航空機のフレームなど)であれば導入の価値があります。
② 製造コストと投資対効果
プレステンパー設備の導入には初期投資が必要です。しかし、長期的に見て製造工程の短縮や材料削減によるコスト削減効果が得られるかを検討しましょう。また、補助金や助成金の活用も視野に入れ、総合的な投資対効果を計算することが重要です。
③ 生産ラインの現状とスペース
プレステンパーは専用設備が必要なため、既存のラインと新設備のスペースやレイアウトを確認する必要があります。設備スペースの確保や、他の生産工程との兼ね合いを検討することで、スムーズな導入計画を立てることができます。
④ 技術者のスキルレベル
プレステンパー工程は温度管理や成形操作など、精密な操作が求められる工程です。自社に熟練した技術者がいる場合はスムーズに導入できますが、そうでない場合は人材育成や外部サポート体制を検討する必要があります。最近では、自動化技術を活用したプレステンパー設備も登場しており、スキル不足を補う選択肢も増えています。
プレステンパーは、自動車、航空機、産業用ロボット、スポーツ用品など、軽量化と高い強度が必要な製品で活用されている技術です。他の熱処理技術と比較しても生産効率に優れていますが、設備導入コストや工程管理の複雑さもあるため、自社の製造ラインや製品特性に応じた導入判断が必要です。
導入にあたっては、製品の要求性能、設備スペース、技術者のスキルレベルを総合的に判断し、補助金や助成金制度を活用してコスト負担を抑える方法も検討しましょう。これにより、品質の高い製品を効率的に生産し、競争力のある製造ラインを構築できるでしょう。
5. プレステンパー導入時の注意点と成功事例
導入時に押さえておくべきポイント
プレステンパーの導入は、単に設備を設置するだけでなく、生産ライン全体を見直し最適化する必要があります。以下は、導入時に押さえておくべき主なポイントです。
① 設備導入計画と投資対効果の検証
プレステンパー設備は高額なため、導入計画の段階で具体的な費用対効果をシミュレーションすることが重要です。初期投資だけでなく、長期的なランニングコストやメンテナンス費用も考慮した上で、総合的なコスト削減効果を検証しましょう。
- ・初期費用:設備費、工事費、人員教育費
- ・運用費用:エネルギー消費、部品交換、メンテナンス費
- ・効果:工程短縮による生産効率向上、材料費削減によるコストダウン
例えば、自動車部品の生産ラインに導入する場合、年間で数十万個の製品を生産する前提で費用対効果を計算し、投資回収までの期間を設定することが重要です。
② 生産ラインの最適化と設計
プレステンパーは複数の工程を一体化した技術であるため、生産ラインの配置や動線設計も見直す必要があります。プレス機、冷却システム、搬送ラインがスムーズに連携できるよう、工程全体を最適化することで、生産効率が最大化します。
③ 設備の安全対策
プレステンパー工程は高温処理を行うため、安全管理が不可欠です。特に、加熱炉やプレス成形時の温度は900℃以上になることが多く、作業員が安全に作業できるように、次のような対策を講じましょう。
- 作業スペースの熱対策(断熱材設置や空調設備の強化)
- 自動化システムの導入による人員接触リスクの低減
- 緊急時停止装置や温度監視システムの設置
プレステンパー導入の成功事例
事例① 自動車メーカーA社:車体部品の軽量化とコスト削減に成功
自動車メーカーA社は、新型車の軽量化を目的にプレステンパーを導入しました。同社では従来、ボディフレームの強度を確保するために複数の部品を溶接していましたが、プレステンパーにより一体成形が可能となり、溶接工程を大幅に削減しました。その結果、以下の成果を得ました。
- ・製品重量の10%削減
- ・年間で生産コストを15%削減
- ・生産スピードの20%向上
A社は、導入初期には金型の耐久性確保に課題がありましたが、金型設計を見直し、冷却経路を改良することで対応しました。これにより、量産ライン全体の品質が安定し、短期間で投資回収を実現しました。
事例② 部品製造メーカーB社:産業用ロボット部品の高精度化に成功
部品製造メーカーB社は、産業用ロボットのアーム部品にプレステンパーを導入しました。従来の製造方法では焼入れ後に歪みが発生し、追加の仕上げ加工が必要でしたが、プレステンパー技術により歪みを抑制し、寸法精度を向上させることができました。
【導入後の結果】
- ・不良品率が従来の5%から1%未満に低下
- ・追加加工が不要となり、1工程あたりの作業時間を30%短縮
- ・顧客からの品質評価が向上し、新規受注が増加
B社は、導入時に技術者のスキル不足が課題となりましたが、外部の技術サポートを受けつつ社内教育を充実させたことで、運用スキルを向上させました。現在では新規ラインにもプレステンパーを導入し、さらなる生産性向上を図っています。
プレステンパー導入後に成功を収めるポイント
① トライアル生産で問題点を洗い出す
プレステンパー導入時は、いきなりフルラインで稼働させるのではなく、トライアル生産を行い、設備の動作確認や品質確認を徹底することが重要です。特に、冷却工程での温度変化や成形精度をテストし、改善すべきポイントを洗い出します。
② 予防保全を徹底する
プレステンパー設備は、高温稼働が続くため部品の摩耗が激しくなりやすいです。予防保全を徹底し、定期的に部品交換やセンサーの点検を行うことで、トラブル発生による生産停止を防ぎます。これにより、設備トラブルの頻度を低減し、稼働率の向上が期待できます。
③ 最新技術の活用
近年では、AIやIoT技術を活用した設備監視システムが普及しています。これらを活用することで、リアルタイムで設備の稼働状況や異常を検知でき、トラブルを未然に防ぐことが可能です。特に、自動データ解析システムを導入することで、生産工程の最適化と異常検知の精度を高められます。
プレステンパーの導入は、設備費用や工程管理の難しさからハードルが高いとされますが、適切な導入計画とリスク管理を行うことで、優れた生産性向上とコスト削減を実現できます。自動車メーカーや部品メーカーの成功事例からも分かる通り、ポイントは適切なトライアル生産、設備メンテナンスの徹底、最新技術の活用です。これらを組み合わせることで、品質の安定化と生産効率の最大化が可能となります。
導入を検討する際には、自社の生産工程や人材の状況に合わせた対策を行い、柔軟に設備計画を立てることが成功へのカギとなるでしょう。